How Does Standard Costing Affect Manufacturing Firms?
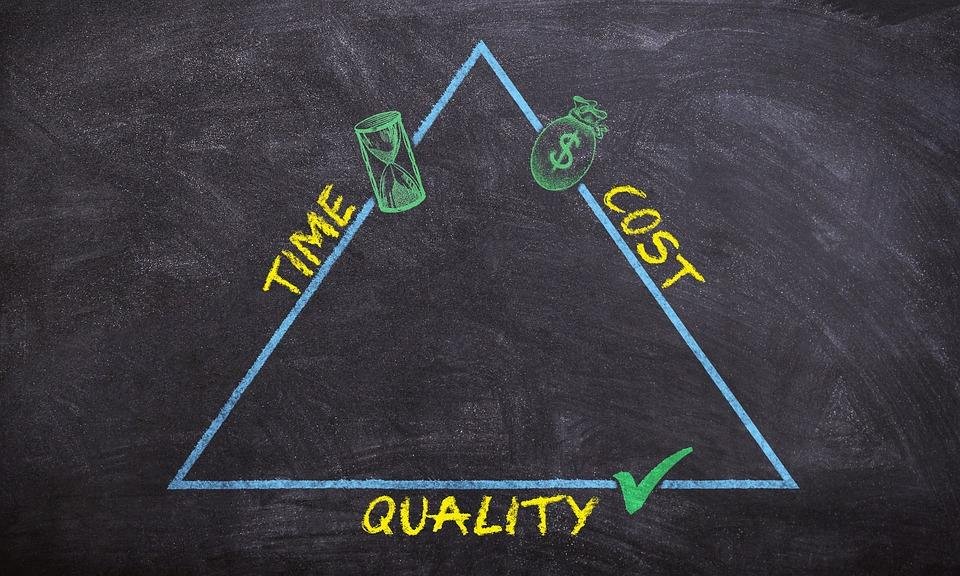
Standard costing is one of the most common costing methods for manufacturing companies. The accounting method has been used by the Ford Motor Company for the mass production of its cars. The practice was soon adopted by other companies as a production cost control method.
Here, you will learn what exactly is standard costing and how it affects the profitability of companies.
Standard Costing: An Overview
Standard costing involves estimating the standard costs of each item. The profit margin is set based on the estimated cost of items. The process of cost estimation involves making assumptions. So, variances normally occur during the execution phase of the project.
Variance refers to the difference between the actual and the standard costs. The variance will be positive if the actual cost is less than the estimated or budgeted cost. In contrast, the variance will be negative if the actual cost is more than the budgeted cost.
Managers need to further investigate the variances. The difference in costs can be due to inefficient operations or errors in estimation. It is important that managers carefully evaluate the variances to know the correct picture.
Types of Standard Costs
Standard costs can be divided into three main categories, depending on the type of costs. These include:
- Standard material costs
- Standard labor costs
- Standard overheads
Material costs refer to the cost of each material. Variances relating to material cost can occur due to the price and quantity of the material.
Labor cost variances can also occur due to different reasons. Variances relating to labor costs can occur due to the labor rate and efficiency.
Similarly, overhead variances can occur due to two main reasons. The variances typically occur due to overhead volume and costs.
Standard Cost Process
The standard costing process starts before the start of a fiscal year. The process consists of a series of events to establish standard costs. The process involves estimating and adjusting costs based on previous financial information.
The management reviews the actual and standard costs to find out variances. The variances are then compared to find out the cause. The information about the product cost is updated based on the ERP software.
The next step involves investigating relevant information to ensure that inputs are properly calculated. The management consults with the production managers to determine the machine hours, direct labor, and overheads that are required for the production of an item.
The costs are broken down into fixed and variable costs. The estimated costs are then entered into the ERP software.
At the end of the period, the management prepares the standard cost report. The report lists the actual cost, rates, and hours. This information is also fed into the ERP. The software calculates the difference between the actual and standard cost highlighting the variances.
Benefits of the Standard Costing Method
The standard costing method allows manufacturing firms to optimize the production process. It helps production managers in multiple ways.
Inventory Valuation
Standard costing allows managers to evaluate the inventory value. The value is calculated and set for each item in the inventory. The standard cost of each inventory is multiplied by the actual amount to find out the inventory value.
The method of valuing inventory using standard costing helps managers in creating a budget. It allows setting a fixed number for inventory valuation that can be used throughout the year.
Using PowerBI and PowerPivot can save time in recording and updating inventory costs using the method. The data input is constantly adjusted to ensure an accurate valuation of inventory with this method.
Budgeting
Standard costing provides fixed values that make it easier to create a budget. The costing method involves setting a budgeted cost for each product. The prices and quantities of items required to manufacture a product are calculated. The quantity and rate are assigned to material labor and overheads.
Budgeting starts for manufacturing companies at the start of each production cycle. This budgeting cycle runs until the production cycle is complete. With standard costing, managers have a fixed cost available at all times that they can use for budgeting purposes.
Determination of Sales Price and Profit Margin
Budgeting also allows business managers to set sales prices and profit margins for manufacturing firms. The standard costing method is used for calculating the cost of goods sold. This allows the management to set a sales price that can help in achieving the desired profitability.
Standard costing also allows the timely preparation of income and loss statements. The accountants can prepare internal profit and loss reports each month using the standard costing method. The management can use the information to make operational corrections to ensure that the company can achieve the desired profit.
Facilitates Performance Comparison
Standard costing also helps in comparing the performance of the staff. The costing method allows business owners to know about employee productivity. The standard labor volume can be compared with the actual output to know about employee performance. The performance of employees can be compared and appropriately rewarded.
Standard costing provides various benefits to firms. But it is also important that the management should know about the shortcomings of this method. Effective use of the standard costing method can help the management to improve internal operations and boost profitability.
Conclusion
Standard costing is ideal for large and complex businesses. But the cost accounting method can also be used by small businesses for cost control. The method allows accountants to create standard costs and quantities for different items.
Management can roll the estimated costs during the next period after making adjustments based on updated cost information. The costing method can help business executives and owners to steer the company while achieving cost and profitability goals.
Maxim Liberty is an outsource bookkeeping service firm. Our team provides virtual bookkeeping services for firms of all sizes and types. If you want more information about our specialized online bookkeeping services, you can contact us by dialing (703) 957-6938.